DXの最前線①~製造業~③
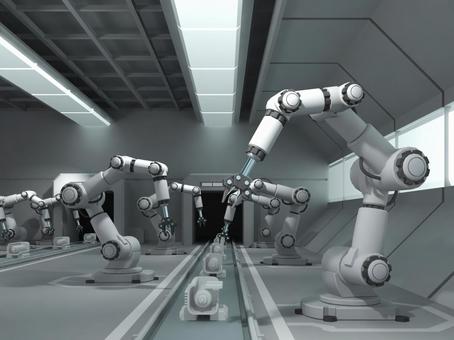
担当:大蔵
皆さんこんにちは!
Frontier Lotusの大蔵です。
前回に引き続き各業界に絞ったDX化の状況や事例を
ピックアップして解説していきます。
今回は製造業における事例をまとめました。
(参照:https://www.meti.go.jp/meti_lib/report/2019FY/000312.pdf)
①オムロン i-BELT (サービス型)
サービス:製造・開発段階で必要な「生産管理」「品質管理」「設備効率」「エネルギー」において現場で状況がわかるサービス
中長期的な視点(取組む目的や経営指標の提示)と、
短中期的な視点(効果が見え、効率化を実感できる取組)の連携強化を支援している。
課題:社内、社外に向けて運用の確立、ものづくりや設計思想と企業文化の融合
その後、標準化に向けたデータの流れを考えることが重要。
データの現状把握→可視化→課題・ゴール設定→業務設計という仕組みを構築
できる人材が、日本に少なくなってきている。
成果:トップの思想と現場の意見をつなげる仕組みを作ることで
製造現場において作業効率の安定化、工具の摩耗量の削減、
加工時間の削減などを実現した
今後の課題:国として、ペーパーレス化などをはじめとした
データ化の基盤を整えていく
②富士通 FCTP (プラットフォーム型)
サービス:
開発チームごとで異なったシステムを使っていたが、このFCTPに一元管理に変更。
製品開発におけるノウハウの共有やリアルタイムでのコミュニケーションが可能になった。
課題:
調達・管理コスト削減、設計者の高齢化・サイロ化による個人差低減、災害対応によるBCP強化のための事業部間の連携強化が必要だった。
事業部ごとに特定の製品を特定の工場で生産しており
事業部間の連携や共通したルールは存在しなかった。
成果:
製品開発プロセスの手戻り減少、品質向上、納期短縮を達成した。
設計段階における不具合抽出、製造しやすい設計の追求が可能になった。
製品開発プロセスのうち、設計から製造に至る部分において、
製造技術部門の業務がデジタル化され、負荷が低減された。
今後の課題:
一社にとどまらない連携など、周辺環境が変化した際にも組み替えて使えるような
汎用性の高いシステム化が求められる。(富士通外に販売していく方針)
③トヨタ 工場IoT (スマートファクトリー型)
サービス:
3D CADデータなど既存のデジタル化データを一元管理でき、
工場と現場などの部署間にまたがる情報共有基盤を作成。
課題:
3D CADデータや試作時の特性データなど、個々の情報のデジタル化を行い、技術開発・生産準備に成果を上げてきた。
しかし実際の製造・お客様から得たデータの技術開発へのタイムリーなフィードバックに苦戦していた
成果:
最初に生産部門と連携し、情報システム部門にてプラットフォームを安全性を確認した上でリリースできるように準備
各事業部・工場にて同様の現場プロジェクトを立ち上げ、IoTの取組の数を増やしていくことで、トータルで費用対効果を上げた。
「工場IoT」で得られた成果を受け、エンジニアリングチェーンやサプライチェーンを含むデジタル化への適用を打ち出し、品質向上や商品力向上、法規への対応等、付加価値向上に関わるデジタル化に着手し始めた。
今後の課題:
デジタル化とセキュリティ対策強化は同時並行で進めなければならないが、自社だけでなくサプライチェーン全体の理解と実施 が必要である。
以上となります。
大手企業の内容が中心となりますが、実施していることは
・自社内で情報の一元管理を行えるように整えた
・そのプラットフォームを通じて改善提案やノウハウへのアクセスを簡易にした。
・企業によってはそのプラットフォーム自体を汎用化し販売できるようにした。
となります。
自社システムを組む、組まないに関わらず
少しでもDXとして取り組める要素があればぜひ参考にして下さい。